Supply Chain Digitization and the Best Metrics to Track
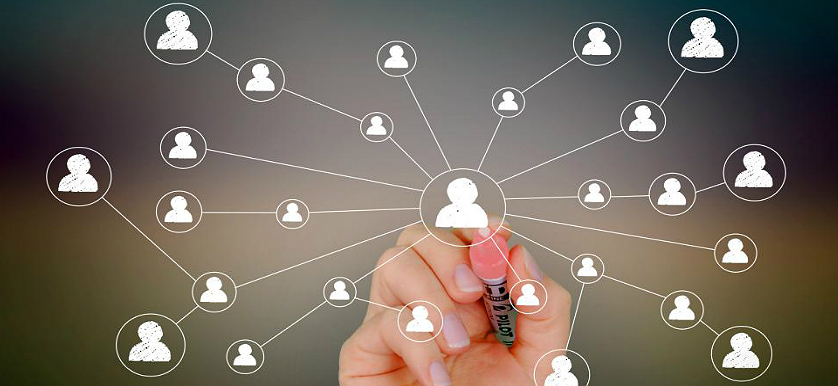
Digitization gives professionals unprecedented access to information that could help them make business improvements. Generally speaking, when you fail to digitize, you’ll deal with a competitive disadvantage.
Supply chain digitization allows companies to be increasingly agile as they meet the needs of their clients and respond to changing marketplace conditions. But why else do companies decide digitization is the right path for them to take?
What Are the Main Advantages of Supply Chain Digitization?
Making your supply chain operate in the digital realm gives you real-time access to information, allowing for proactive decision-making. The dashboards used within digital supply chains help managers dig into the data and find where weak points exist.
The information also permits a more granular look at parts of the supply chain. For example, the connected sensors on freight trucks can show precisely where an individual vehicle is at any point. Or, it can help a company verify that perishable items always stay within the required temperature range. Having access to such data builds trustworthiness when engaging with customers or suppliers.
Many digital supply chains also feature robotic components. They promote efficiency and provide more consistent results for supply chains. Since machines don’t get tired or need breaks, they can adequately supplement human efforts to get things done. Often, when supply chain companies want to scale up, they use robots to help them achieve that goal.
Digitization enables supply chain companies to avoid waste, too. More specifically, representatives can drill down into metrics and track them over time, examining history to determine what’s working well and what isn’t. Here are six of the best metrics to track when embracing supply chain digitization.
1. Percentage of On-Time Delivery Since Automation
The on-time delivery metric measures how often a supply chain business meets its delivery promises. However, customers and supply chain companies must agree on the specifics of what on-time delivery means. For example, does any leeway exist within the delivery date? Some enterprises provide an extra two-day window to account for unforeseen circumstances.
Or, what happens if a customer buys multiple items within one order? Is the delivery only on time if all the products in the order arrive by the promised date? After ironing out the specifics of the on-time delivery measurement, supply chain companies are then in a prime position to set up their digital systems to gauge how their performance improves over time.
More specifically, they should compare and contrast the differences made by any automated additions to their supply chain. Has the overall on-time delivery metric gone up since a company started using automation or another digitization strategy? Bear in mind that the benefits will probably not be immediately apparent, which means firms must allow time to adjust to the automation.
2. Reduction in Greenhouse Gas Emissions
Numerous factors can make a company’s representatives decide it’s time to move forward with plans to digitize the supply chain. However, businesses usually prioritize specific aims. For example, Cisco is focusing on sustainability when digitizing its supply chain.
It wants to cut out 1 million metric tons of greenhouse gas emissions from the fiscal year 2012 to fiscal year 2020. Part of the brand’s digitization efforts involve working with all its manufacturing partners to reduce emissions through various actions. Supply chain entities can’t make any associated changes if they don’t have baseline metrics first.
Digitization can provide those numbers, giving companies constructive guidance on how to change and which issues are the most substantial. The metrics given through digitization can also keep supply chain partners motivated, such as by showing the sustainability achievements made from year to year.
3. Percentage of Reactive Maintenance Performed
There has been a 76% uptick in the number of supply chain professionals reporting they use predictive maintenance, a recent report shows. Companies have many options for applying predictive maintenance to their business models. But, a key performance indicator that shows the payoff of such efforts is the percentage of reactive maintenance undertaken.
That’s a measurement General Electric suggests watching during a digital transformation. In other words, how much time is your supply chain spending on maintaining equipment before it breaks down, versus repairing something once it no longer functions?
After you get the percentage of reactive maintenance nailed down, applying that metric to learn other things then becomes much more straightforward. For example, you might determine how much your company saved through digitization investments that allowed for improved predictive maintenance.
4. Rate of Inventory Turnover
A company’s inventory turnover is a ratio that shows the number of goods sold and replaced during a defined period. Having a high ratio indicates either strong sales or insufficient inventory.
Conversely, a low ratio usually means poor sales or having an excessive amount of sellable goods on hand. Issues where things are consistently out of stock or available in surplus could create significant imbalances that hurt supply chain performance due to a lack of inventory visibility.
If companies choose to examine this KPI during their supply chain digitization, they should be well-equipped to make better-informed decisions about when to replenish supplies or deal with the fluctuating demands of an ever-changing marketplace. Having that kind of awareness could prevent inventory issues that cause significant disruptions.
5. Percentage of Cyber-Assessed Connected Suppliers
The Digital Supply Chain Institute released a report to clarify some new metrics brought about by the digitization trend. One of them is the percentage of connected suppliers who have gone through a cybersecurity assessment.
A McKinsey & Company article from 2019 goes into detail about the need for risk management in an increasingly connected world. It suggests that supply chain representatives take the time to catalog the full scope of risks they face. Part of that task involves creating an integrated risk management framework comprised of three areas:
- The impact on the organization if the risk materializes
- The likelihood of the risk materializing
- The organization’s preparedness to deal with that specific risk
Consider that a risk faced by any member of your supply chain could also derail your internal operations. With that in mind, you could create a cybersecurity checklist for each supply chain party that uses the internet for its business. You may initially find most of the companies in your supply chain have severe cybersecurity shortcomings to fix.
In that case, set a realistic deadline for resolution. If a partner does not meet it or otherwise shows a lack of commitment to preventive cybersecurity measures, it may be time to stop working with them.
6. Percentage of Operations Handled Manually/Through Automated Technology
Supply chain digitization should not happen hastily. Instead, your company should recognize the value of making the changes slowly and purposefully.
Not every supply chain-related responsibility is appropriate for digitization. However, if your company wastes too much valuable time through manual processes, it’s time to revisit those areas and look for better solutions— like those the digital realm could offer.
Take the example of Mitchells & Butlers, a company that runs restaurants and bars in the United Kingdom. Before using automation, the company needed 3 million pieces of paper each year to tackle all its manual processes. After incorporating automation for some requirements, the company saved more than 20,000 hours of employee hours and found it could identify errors much earlier than before.
Selecting the percentage of your operations done by hand or through automation could help you measure the overall digitization process over time while letting you justify expenses. What if your percentage of automated operations went down by 10%, despite your company investing twice as much on automation this year versus the last?
Such evidence would indicate something’s going wrong in your digitization strategy. But, after acquiring the manual versus automated task percentages, take a closer look. Maybe you’ve only digitized two new processes in a year, but those changes led to a 60% reduction in error rates. Only looking at the automation percentage would cause disappointment, which is why it’s necessary to look at the relevant effects, too.
Personalize Your Supply Chain Digitization Strategy
Supply chain companies often make mistakes as they attempt to digitize their processes if they focus too much on which KPIs other companies track or what generalized industry advice recommends they should do. The best approach to take is to examine the internal needs of a company and explore how digitization could help address them.
It’s virtually pointless for a business to invest in supply chain digitization without first having a plan for how, why and when they’ll do it. The answers to those questions only come after enterprise representatives scrutinize their firms and remain unafraid to make some potentially dramatic changes.
Image sources:
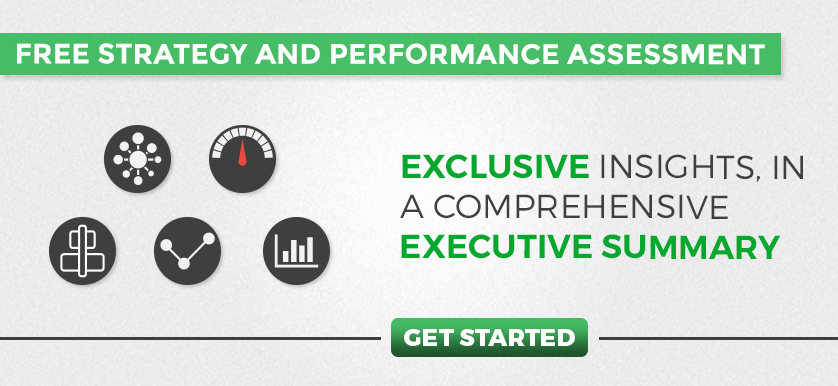
Tags: Green Business, KPI, Supply Chain Performance